Cookstown firm, Cemcor is 'becoming an industry leader' by investing over £6million in sustainability
and live on Freeview channel 276
After acquiring Lafarge Ireland in 2022, Cookstown Cement rebranded to Cemcor following significant investment from the new local ownership of managing director, David Millar and LCC Group.
In 2023, Cemcor has invested an additional £6million in multiple industry-leading upgrades, focused on the sustainability and futureproofing of the plant.
Advertisement
Hide AdAdvertisement
Hide AdImmediately after the purchase of Cookstown Works completed, Cemcor pledged over £6million to replace the existing electro-static precipitators (ESPs) with a state-of-the-art bag filter at the plant.

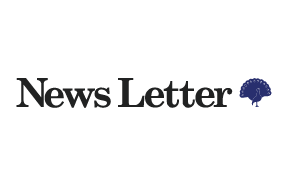
Within a period of 14 months from final design agreement in March 2022, the new bag filter was commissioned and fully operational from May 2023.
The top of the range filtration has is a Tribor System which detects and locates damaged bags. This system will isolate the cleaning operations to a specific row and if the damage is minor, reseal with process dust. If the bag is severely damaged, Cemcor’s new bag filter has the ability to isolate the entire section and online maintenance can be carried out, making it a much more efficient operation and reduces wastage.
Conscious on its outputs to the environment, Cemcor also installed a new dust particulate conveying system at the Cookstown plant.
This system will transport the captured dust to an existing silo via a new batch weighing feeder where it will be recycled through the cement manufacturing process, so no material is landfilled or disposed elsewhere.

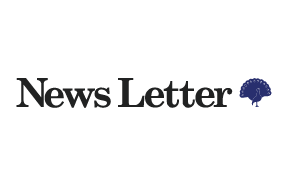
For sulphur dioxide abatement and the neutralising of other process gases such as chlorine, Cemcor installed a reaction tower in 2023 with hydrated lime injection from a dedicated silo as well.
Advertisement
Hide AdAdvertisement
Hide AdProcess gases will be directed from the kiln system through the filter prior to clean gases being released via the stack due to the instalment of a new 750KW main process fan as well.
Cemcor managing director, David Millar, said: “We are delighted with the huge leaps forward Cemcor has made with regards sustainability and efficiency upgrades since the acquisition last year.
“The plant itself looks and operates at an extremely high standard, which is a credit to the whole team involved in these projects. We are forward thinking at Cemcor and understand it was time to put our money on the line and invest in the plants efficiencies and sustainable outputs, to protect the environment around us and futureproof the plant itself.”

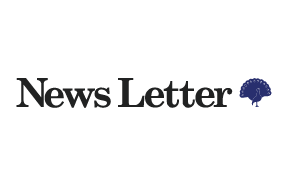
With a well-rounded view on plant upgrades, Cemcor also focused its research on how the paper packing market of cement bags has been developing in recent years. After an in-depth review of its paper packing system and research into material developments such as recyclable and biodegradable paper options, Cemcor invested in both new hardware and software upgrades to its paper packer. These upgrades have already provided efficiency benefits through improved reliability and consistency as well as improving the ease of operations through a new touchscreen operating system which has built in diagnostics and remote support access.
Later this year, Cemcor will also replace the existing manual pallet wrapping process with automated stretch hood equipment, ensuring the plant is as efficient as possible. Further upgrades, similar to those carried out on the paper packing line, have been planned for the plastic packing line in the near future.
Not settling for complacency in any area of the company, Cemcor is also investing in new laboratory equipment to improve the speed and accuracy of the raw feed analysis, including online monitoring and new handling facilities for alternative raw materials including biogenic carbonates.